Computer Numerical Control (CNC) is a revolution of this modern manufacturing by the automatic control, movement and machine tools through the programmed computer software embedded in the machines.
This technology is the most important for manufacturing the metalic and plastic parts. This is one of the latest and advanced method to proper use of automate the operations of tools such as mills,lasers, lathes, routers, grinders, drills and water jets. This system also extend to the non-mechine tools like welding, electronic assembly and filament winding machines.
How does CNC Works?
Every object made in a CNC has its unique computer codes which are normally written in G-code, that are kept in and carried out by Machine Control Unit (MCU). Movement of the machine is controlled by G-code just as the functioning in general, while M-code does outside activities. These codes involve directions for the machine tool, including feed rate, position and tool speed/not necessarily these .
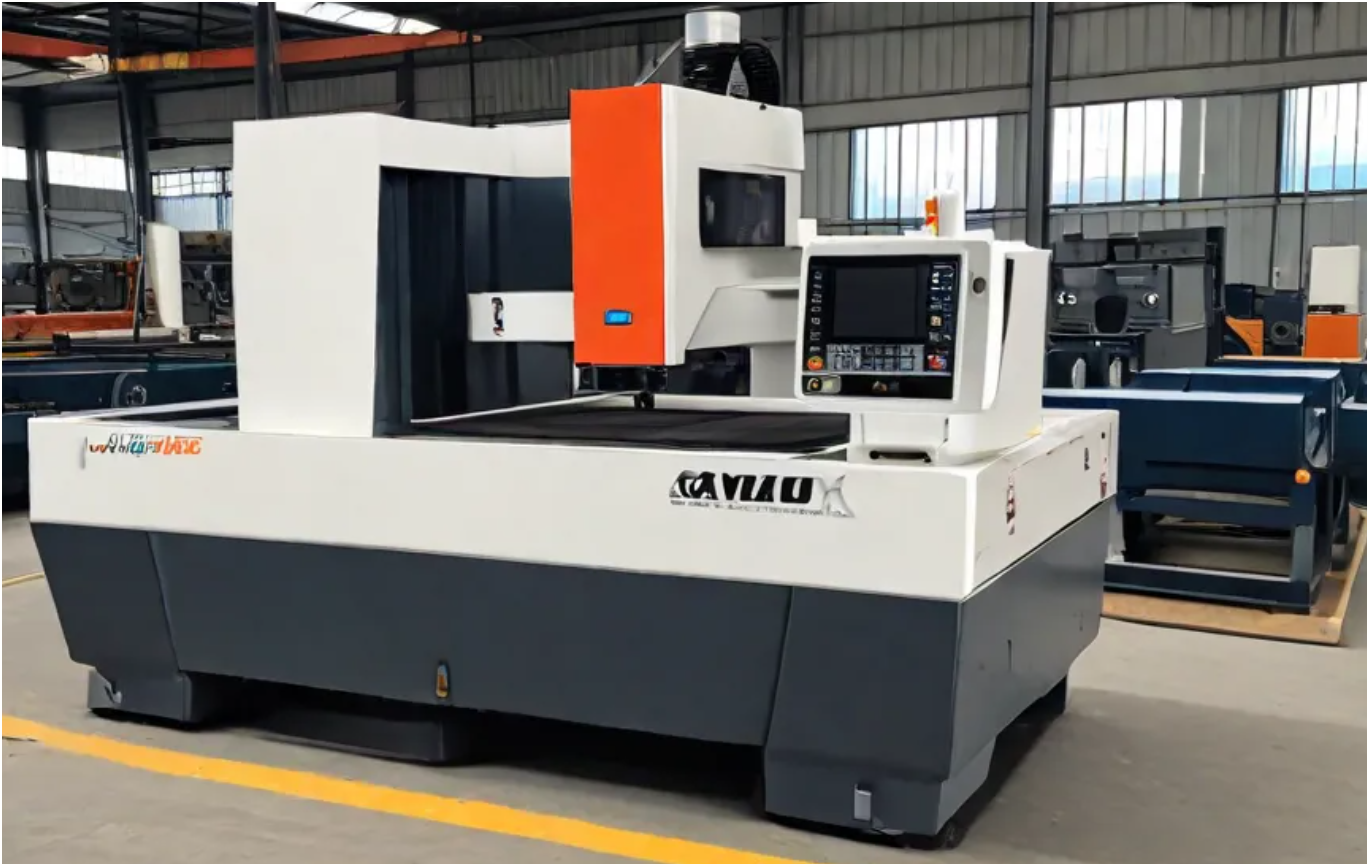
Engineers typically begin by making a Computer-Aided Design (CAD) that shows all the details of the object which has to be produced. Next, they convert this drawing into G-code that is put on the MCU. Thereafter, the operator tests it while no raw material is present so as to ascertain its rightness. After this, a Computerized Numeric Control (CNC) machine takes over to execute the program achieving things like creating components from scratch and also making precise cuts or prints.
History of CNC
It can also be traced as far back as 1949 with John Parsons‘ invention of the first numerical control machine. In 1952, MIT researchers developed the first commercially available CNC machine, the Cincinnati Milacron Hydrotel. In 1958, the first patent for a CNC machine heralded the birth of this technological revolution into a full-blown manufacturing technology.
Benefits of CNC Systems
- Cost Reduction: CNC machines benefit a company by improving efficacy henceforth resulting into lower operating costs following a decrease in energy used for production as well as cutting wastage alongside associated negative effects. In addition, they also have aftereffects on financial liabilities with regards to workers protection and security.
- Waste Reduction: This CNC Software simulations and optimize the result in minimal waste during the manufacturing process.
- Improved Worker Safety: This system could lower the risk of various accidents and ensure the safety of the workers.
- Human Error Reduction: CNC could eliminates human error and providing greater precision, complexity, speed, flexibility, and repeatability. Although this human error reduction is one of the milestone changes to this platform.
- Contour Machining: With CNC you can mill out contoured shapes like 3D printed pictures.
- Faster MCU Programming: Integration of MCU programming is accelerated by the Computer-Aided Manufacturing (CAM) and CAD software.
- Improved Operational Intelligence: It improves operational intelligence with ERP and EAM integration, which in turn enables better plant performance.
- No Bottlenecks: CNC systems reduce production bottlenecks, hence improving the manufacturing outcome.
CNC Use Cases
Aerospace
Computer Numerical Control machining has become very imperative in delivering the best level of precision for mission-critical components in the aerospace industry, such as landing gear, titanium shrouds, and airfoils. Aluminum and stainless steel are used, as well as titanium and high-performance alloys.
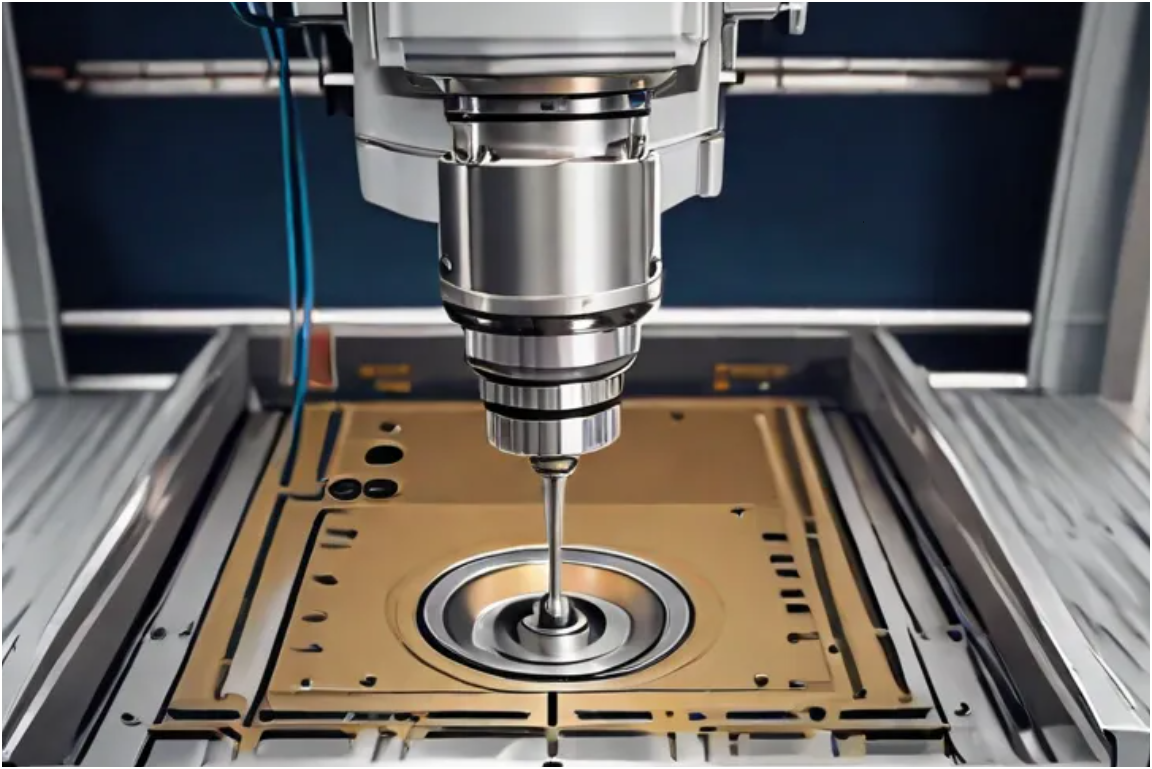
Medical Equipment
The medical sector is also dependent on CNC for customized, accurate, and high-quality products, including MRI machines, implants, orthosis, and research apparatus. CNC therefore served very importantly in the production of medical products quickly at the level of the pandemic caused by COVID-19.
Automotive
They are also used in the automobile industry for prototyping and producing parts neighbourhood to gearboxes, engine components, valves, and dashboard panels.
Electronics
It is applied in the manufacture of electronic components like semiconductors, printed circuit boards, heat sinks, amplifier housings, etc.
Oil and Gas
Computer Numerical Control machines ensure that large machinery parts used in drilling rigs and refineries, such as drill bits, rods, pistons, and valves, fit accurately.
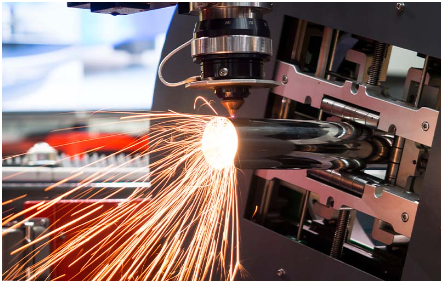
Marine
Such can be the varied demands of Computer Numerical Control precision parts in the marine industry. Which is ranging from propellers to insulating cases, engine components, or even prototype molds in keeping ships operational.
Through the integration of CNC technology, industries have achieved unprecedented levels of precision, productivity, and safety. If you have any messages or suggestion for us, you can email us. Thank you.